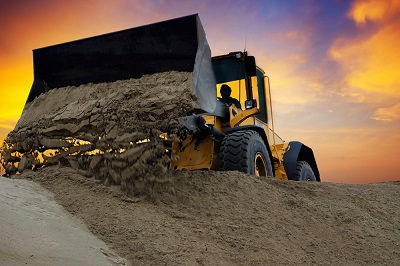
Big Bertha finally made its way to the light in Seattle last week. An engineering marvel to be sure, but a costly one with nearly 3 years of project delays. While your equipment is likely smaller and you probably won’t hit a buried pipe, unscheduled downtime of your equipment will increase your costs and slow your project down.
I think no one would disagree that preventative maintenance can save you money in your construction business if the alternative is unscheduled downtime. So what are three areas that you can reduce costs with the proper preventative maintenance?
Reduce the cost of labor by improving your productivity and reducing overtime
Reactive maintenance is often emergency maintenance, particularly if it happens on a job site or when you are about to dispatch a piece of equipment. The more reactive maintenance you have to do, the more likely you are to incur overtime costs and the less likely you are to be able to predict and control your staffing levels.
Preventative maintenance allows you to plan and stagger your maintenance events to eliminate peaks and troughs within your labor requirements. It also means you can prioritize based on future forecasts, utilization, and seasonal trends to make sure that you are less dependent on overtime and emergency work. Most importantly if you track not only your average times for each type of maintenance event you can compare against manufacturer’s recommendations and predict more as you develop your PM planning going forward.
If you could reduce your overtime bill by just 10% how much would that save you month over month?
Control your parts inventory and reduce emergency parts deliveries
When you are dependent on reactive maintenance, the chances are that you’ll find yourself ordering a great many parts for overnight delivery or emergency shipping. This is very expensive and can change the cost of a part from a few dollars to 10 or even 20 times that! As well as leaving your equipment unavailable as it waits for new parts, the cost of the repair is far greater than it ought to be. Sometimes this is a hidden cost if transportation and overnight shipping fees are tracked separately in the ledgers and you don’t quite see the number. In other cases, your cost of goods suddenly shoots through the roof as your accountants insist on costing the part plus its cost of transport.
Preventative maintenance should allow you to determine the normal expected parts requirement for any normal service. So for example, if you know a 3-month service for a telehandler requires the replacement of 4 air hoses, then you can make that the right hoses are available before the scheduled maintenance date.
If you could simply make sure that the right parts were always on the shelf how much money would that save you? If you could reduce the cost of emergency / overnight parts shipments by just 20% what would the monthly improvement be? If you could reduce the number of days equipment sits in an “awaiting parts” status and is unavailable for use by 50% what would the effect be on your need to rent or transport equipment from other locations? How much might that save you?
Reduce breakdowns in the field
Nothing is going to prevent your job sites from occasionally damaging the equipment through bad practices or genuine job-site accidents. However, you can prevent job-site breakdowns caused by equipment that hasn’t been maintained properly. As well as the cost of emergency call outs, the potential need to organize swap-outs of equipment to get the site up and running again and the huge cost of logistics this may entail.
If you could reduce the need for job site emergency call outs by just 20% what might that save you in technician costs? If you could cut the number of swap-outs due to breakdown (as opposed to customer damage) but just 10% how much might that save you in logistics costs every month?
If you are looking for software that takes into account maintenance schedules and preventative maintenance, let us show you how Wynne’s preventative maintenance programs can reduce your costs and improve margins.