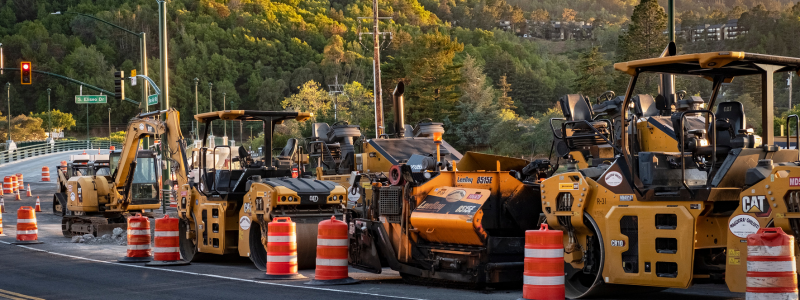
Managing consumables, tools, and equipment across multiple job sites and storage locations presents a significant challenge for large construction companies. This is especially true for companies with either no construction equipment management software, or a software not built for large companies with multiple warehouses and job sites. Without an optimized approach, inefficiencies lead to financial losses, productivity setbacks, and operational disruptions. Delays in locating equipment, over-ordering of materials, and miscommunication between warehouse and field teams slow down projects and impact overall profitability.
According to the Construction Industry Institute (CII), up to 30% of materials delivered to construction sites go to waste due to poor planning and inefficient inventory management. The National Equipment Register (NER) estimates that $300 million to $1 billion worth of construction equipment is stolen annually, with less than 25% of it ever recovered. These inefficiencies highlight the urgent need for better asset and consumables management across multiple locations.
As construction projects increase in scale and complexity, businesses must refine their inventory management strategies to ensure tools and materials are available when and where they are needed. A proactive approach to inventory control not only reduces waste but also enhances project efficiency, keeping timelines and budgets on track.
Challenges of Managing Equipment Across Job Sites and Warehouses
- Lack of Real-Time Visibility
Tracking tools and consumables in real time is nearly impossible without a centralized system. Construction teams often rely on manual tracking or outdated spreadsheets, leading to miscommunication, misplaced tools, and costly project delays. Without a clear picture of available inventory, job sites experience unnecessary shortages or delays in receiving materials.
Andrea Upah, who manages purchasing and inventory at Big D, explains, “Rental Result makes it very easy. I can handle things from my desk. I don’t have to necessarily walk into the warehouse where everything is stored to physically see what I have on hand. I can easily check my inventory stock on the computer, and it tells me exactly what I have, where it’s at, if it’s located here at this yard, if it’s over at our secondary yard for larger items.” This level of visibility ensures teams can act proactively instead of reacting to shortages.
- Inefficient Replenishment Processes
Balancing inventory between warehouses and job sites is a common struggle. Poor planning and mismanagement lead to overstocking in some locations and shortages in others. This imbalance increases project costs, wastes valuable materials, and creates inefficiencies in field operations. Without a structured process for ordering and restocking consumables, projects can suffer from unpredictable inventory levels, forcing teams to make costly last-minute purchases.
Andrea highlights how historical data can improve replenishment: “I can go back and look at the history of things purchased. I can go back and see like if we’ve sold extension cords in the last six months or how many I’ve sold within the last year.” Having access to purchase history allows teams to forecast accurately, reducing waste and ensuring critical items are always available when needed.
- Theft and Loss of Equipment
Construction sites are highly vulnerable to theft and asset misplacement. Without proper tracking, tools and equipment can be lost in transit, misplaced on job sites, or even stolen. The lack of real-time asset tracking leads to millions of dollars in lost equipment annually, impacting budgets and productivity. Establishing tighter controls over tool checkouts and returns significantly mitigates these risks.
Andrea underscores the importance of accountability within inventory systems: “There’s a cookie crumb for everything in there. Even if I touch something in inventory or adjusted it, it tells me exactly when I did that or vice versa if anybody else has been in there.” This level of tracking not only prevents losses but also ensures that every tool and material is accounted for.
- Manual and Paper-Based Tracking
Traditional inventory tracking methods, such as paper logs and spreadsheets, are highly prone to errors. Manual processes lack accuracy, and locating critical assets becomes time-consuming and inefficient. Studies show that 35% of construction professionals spend over an hour per day searching for missing project data, contributing to project delays and increased labor costs. Modern construction projects demand automation to keep pace with the fast-moving nature of job sites and prevent unnecessary downtime due to missing or misplaced assets.
Best Practices for Managing Construction Equipment, Consumables, and Tools
- Implement a Digital Asset Management System
A centralized asset management system is critical to gaining full visibility over equipment and consumables. These platforms provide real-time tracking and reporting, allowing construction teams to make informed decisions about asset allocation. By digitizing inventory control, companies reduce waste, increase efficiency, and ensure that critical materials are available when and where they are needed.
Andrea describes how technology has made processes more efficient: “I have different warehouse workers that can easily access in their tablets exactly what everybody has ordered and get that picked in a timely manner. It’s as easy as clicking buttons.” A centralized system ensures consistency across all locations and reduces reliance on inefficient manual processes.
- Use RFID and Barcode Scanning for Automated Tracking
Modern inventory management solutions utilize RFID tags and barcode scanning to streamline asset tracking. These technologies reduce human error, provide precise location data, and help teams keep track of every tool and consumable as they move between warehouses and job sites. With automated check-in/check-out systems, accountability increases, and the risk of lost or stolen assets decreases.
- Develop a Centralized Ordering and Allocation System
Construction firms must establish a standardized process for ordering, storing, and distributing consumables and equipment. A centralized ordering system ensures that project teams access the resources they need without creating inventory imbalances. This approach improves forecasting accuracy, reduces procurement costs, and eliminates unnecessary purchases.
- Enforce Structured Check-In/Check-Out Processes
Establishing a clear process for checking out and returning tools enhances accountability and minimizes losses. Digital check-in/check-out systems, such as mobile apps and on-site kiosks, allow teams to track who is using specific equipment and when it is due for return. This structured approach prevents misplacement and unauthorized use of valuable tools.
- Optimize Just-in-Time (JIT) Delivery for Consumables
Overstocking job sites with excess materials leads to waste, while understocking results in delays. Implementing a Just-in-Time (JIT) inventory strategy ensures that materials arrive precisely when needed, eliminating unnecessary holding costs and minimizing waste. Construction companies that adopt JIT strategies see improvements in cash flow and inventory turnover rates.
- Conduct Regular Audits and Cycle Counts
Routine audits and cycle counts prevent discrepancies in inventory records and ensure that consumables and equipment are accounted for. Regular assessments of stock levels in warehouses and job sites allow teams to address shortages before they disrupt operations. Automated audit systems make these processes more efficient, reducing manual effort while improving accuracy.
- Improve Communication Between Warehouse and Field Teams
Streamlined communication between warehouse staff and job site teams prevents delays and ensures that assets are delivered where they are needed most. Mobile communication tools and automated notifications provide real-time updates, keeping teams informed about equipment availability, delivery schedules, and replenishment requests. When warehouse and field teams are aligned, inventory management becomes a seamless process.
Finding the Best Construction Equipment Management Software.
For construction companies looking to improve inventory control, now is the time to take action. Implementing software for managing construction equipment, structured inventory processes, and real-time communication tools will drive greater efficiency, reduce waste, and create stronger project outcomes.
RentalResult provides the solutions construction firms need to streamline operations, reduce asset losses, and improve efficiency. Contact us today to see how our platform will transform your equipment and inventory management.