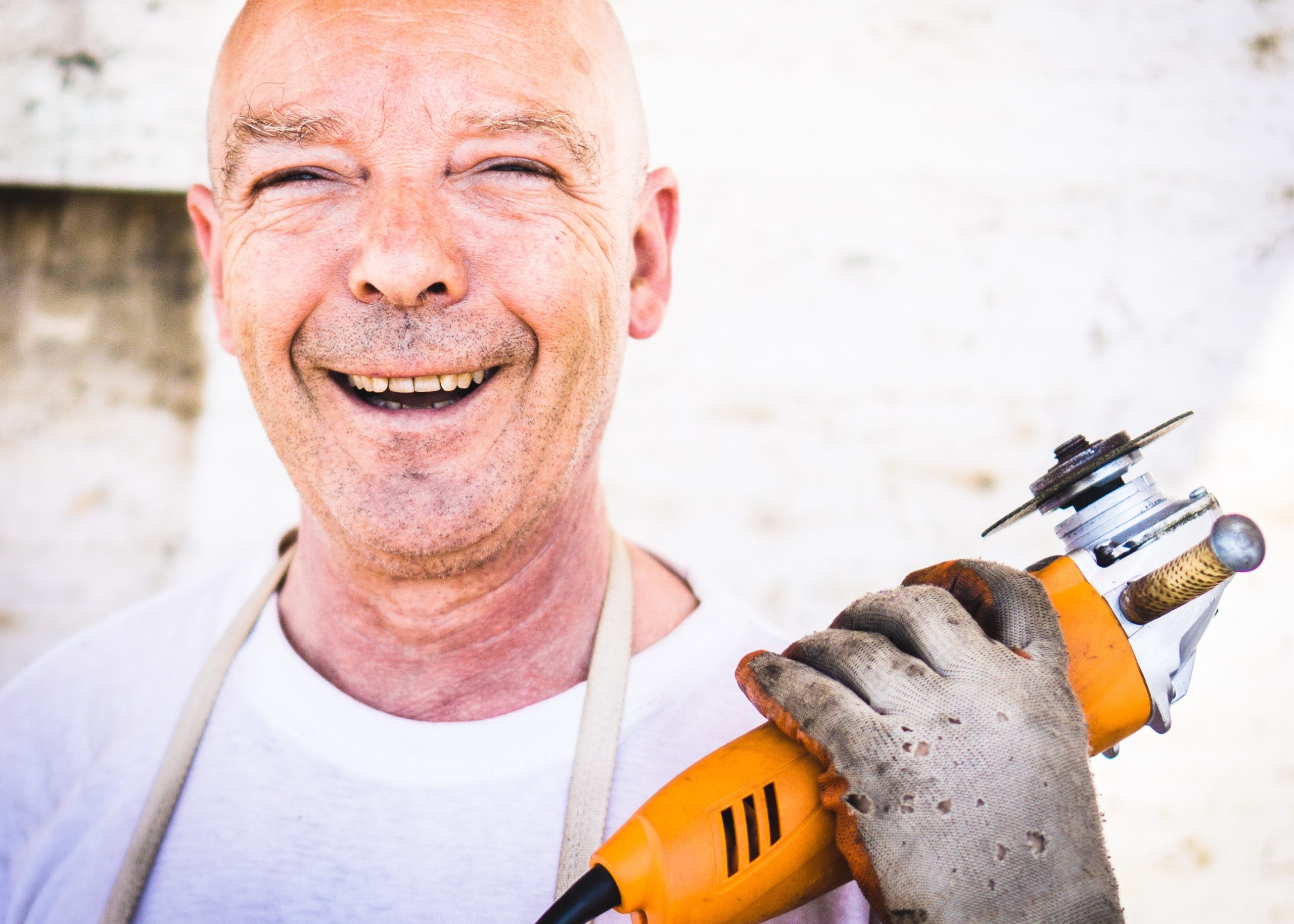
Tool tracking is both a technology and a process challenge. The technology challenge is being solved by an increasing number of manufacturers who are adding RFID tags to their tools. This allows you to physically track where your plant and tools are on the job site. However, RFID doesn’t solve the process challenge. It’s all very well for you to know that the tool was assigned to Ryan at 10am on Project X from your tracking software. It might also be helpful to see on a map where that tool is if you have GPS or a mesh network set up. But what about all the other business activities that fall around the process of tracking tools?
How did the tool get there?
It’s great to be able to find out who has a tool, but what about how the tool got there? Did the job site go and pick something up from the nearest Home Depot, or did they order through your procurement team and potentially get better discounts for volume purchasing? If they got it from you, how did that happen: a phone call, an email, or a field requisition? Can you take a field requisition and use it to trigger your fulfilment processes automatically or in a way that reduces double entry and possible errors? Did you need to use your own transport, or was it delivered by a courier or picked up from the warehouse by the site foreman? These are all questions that tool management software should be able to address.
Inventory discrepancies of your tools
Is your tool tracking system designed to manage your inventory? Tool tracking at the job site is not the same as tracking how many tools you have, where and how they can be deployed. If your tools are sitting in your warehouse, do you know how many you have, what status they are in, and are they ready for deployment or need repairs? Can you transfer your tools easily from one warehouse to another or does that require lots of manual updates to individual tool records? When you find a discrepancy is there a proper way to manage it? Do you simply delete a tool or add another one to make things balance with no link to asset registers, inventory management or your other corporate applications? Inventory management should be a key part of your tool management software.
Reservations and future deployments of job site tools
Tool tracking is generally treated as a very immediate process. Where is my tool right now? But what if your job site is going to kick off in 2 weeks? Then you need to be able to plan what tools will be deployed on Day 1. In this instance, it’s not a question of can I ask for another 10 hammer drills tomorrow, it’s a question of can I get 500 tools deployed in 2 weeks? Being able to plan for tool deployments allows you to maximise the potential of your existing tool stock. It allows you to buy efficiently when you need a top-up and re-use existing tools to maximise your utilisation over the life of a tool. Being able to plan for that in your tool management system rather than trying to keep track off-line in spreadsheets creates both value and efficiencies in your plant and tool depots.
Tool hogging: It’s mine, you can’t have it!
Once a job site has a tool, the chances are they aren’t going to relinquish it, even if it’s not being used. Here’s where active tool-tracking, using GPS or telematics can be incredibly powerful. They allow you to tell the job site that 25% of their plant and tools are sitting idle. But if you can’t make the financial case for tracking your tools automatically, you can still use all the data in your tool management system. You can track how many tools have been delivered to the job site, how many people they have and compare the ratio of tools to people. You can at least show the site foreman or the project accountant just what each of those tools is costing them in an easy to access, real-time format. If you can reduce the number of unnecessary additional deliveries or reduce the number of idle tools on the job site, it has the potential to directly improve your margins.
Tool tracking is more than simply knowing where the tool is right now. It’s about being able to plan, schedule, deploy and manage a large inventory of objects across multiple job sites and multiple depots, reducing the need to use external re-hire suppliers.