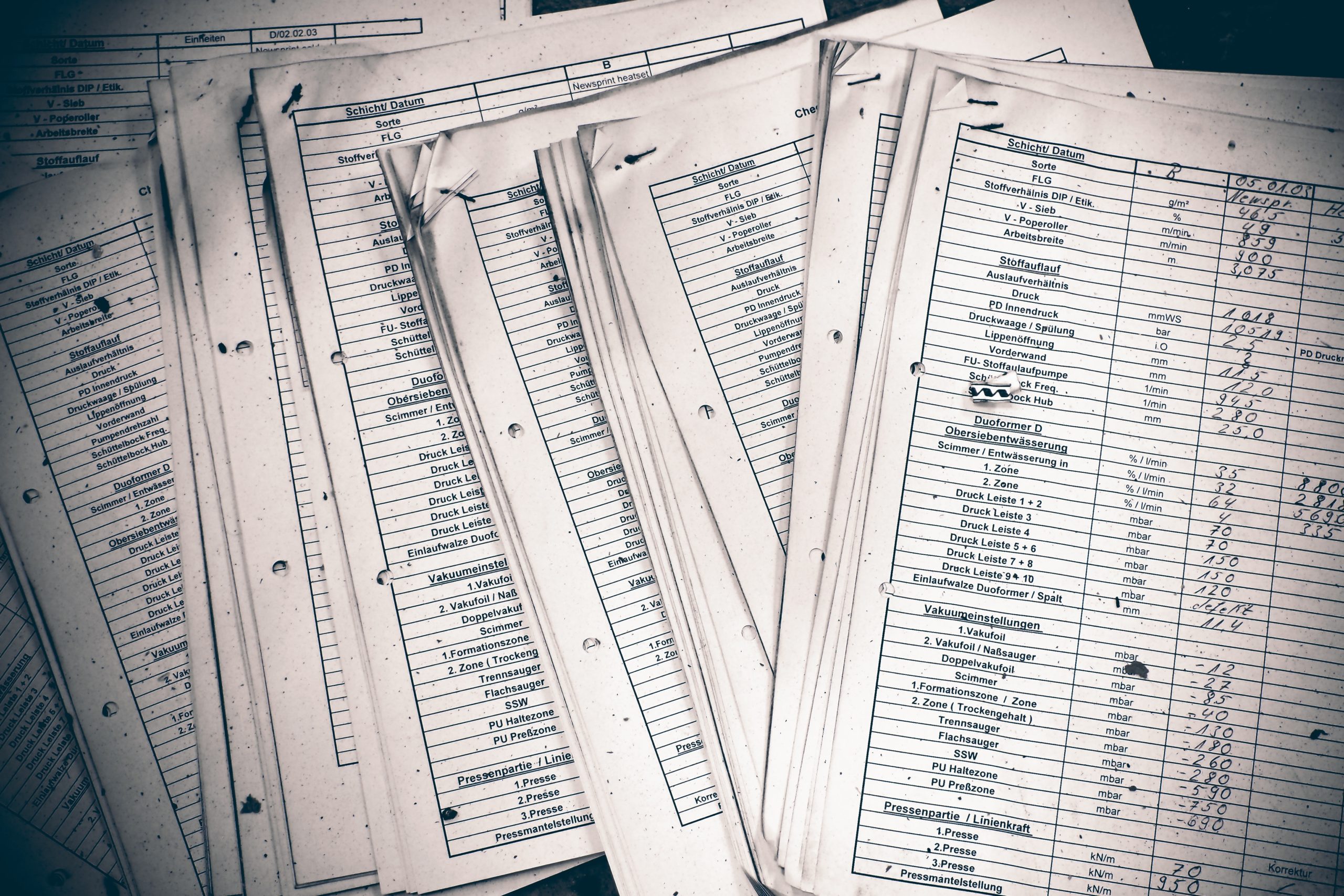
Whether you’re implementing a new ERP or maintaining your existing solution, if you put rubbish in, you’ll get rubbish out. In both scenarios, ensuring your data remains squeaky clean is of the utmost importance. Carrying out regular job site audits is an effective method of upkeeping your data quality.
With specific regards to plant hire, consider how often equipment comes and goes on a daily basis. Equipment moves from site to site, gets lost, damaged, and “borrowed.” If you’re still using a spreadsheet to manage all that, this blog post should hopefully illuminate a much better way.
In addition, mobile apps have completely revolutionised the way physical audits can be carried out on job sites. With just a phone or tablet, managing plant and equipment on a daily, weekly, and monthly basis to ensure safety and compliance can be seamlessly integrated into your regular routine.
Here are our top eight tips to carry out an effective site audit to achieve an accurate ERP database.
#1 Communication is Key
Well before the actual day of the audit, make sure all of your site teams and subcontractors are aware and prepared. Communicate where everyone needs to be at what time via tool box talks and site notices. Direct line managers should be present to help coordinate efforts on the day. Most of all, stress the importance of the audit and the reason why you’re doing it.
#2 Lock Down Your Job Site
Once all of your essential personnel have arrived to your job site, lock the gates! Chasing people entering and leaving a job site can be a logistical nightmare, so ensure that nobody leaves until your audit is complete.
#3 Consider Your Business Partnerships
While many businesses work in strategic partnerships nowadays, such cooperation increases risk of loss and data anomalies. If you share a yard, make sure to audit all vans and stores.
#4 Make PUWER Part of Your Asset Control Process
Provision and Use of Work Equipment Regulations is a HSE directive for ensuring equipment is fit for use that is achieved through regular on-site equipment checks. Software solutions can make following that directive a lot easier. Choose an application that can manage breakdowns, condition reporting, hire visibility, and hire requesting all from one system.
#5 Expect the Unexpected
Audits have a tendency to uncover all manner of unusual findings. Equipment previously marked as lost just might reappear. You might also find equipment so old that it no longer has a serial number (due to it being disposed of in a parent ERP system).
#6 Go Beyond Recording Serial Numbers
A physical audit is so much more than marking serial numbers against item descriptions. Record where you found an item and who is currently using it.
#7 Make Immediate Use of Your Data
The hire industry is fast-moving. Once an audit is complete, make sure to process all data in to your ERP to get the maximum benefit of your hard work and effort.
Doing so will save money and maintain safety.
#8 Make Bold Decisions
If you’re unable to locate an item on-site, it’s incumbent on you to make decision. Is it best to leave it on hire and hope it turns up elsewhere? Should it be moved into a “quarantined status” while still being paid for? Would it be best to mark it as lost and negotiate a settlement fee? These are all important questions that businesses need to respond to. However you choose to answer such scenarios, an accurate equipment list is sure to drive efficiencies and provide cost savings.