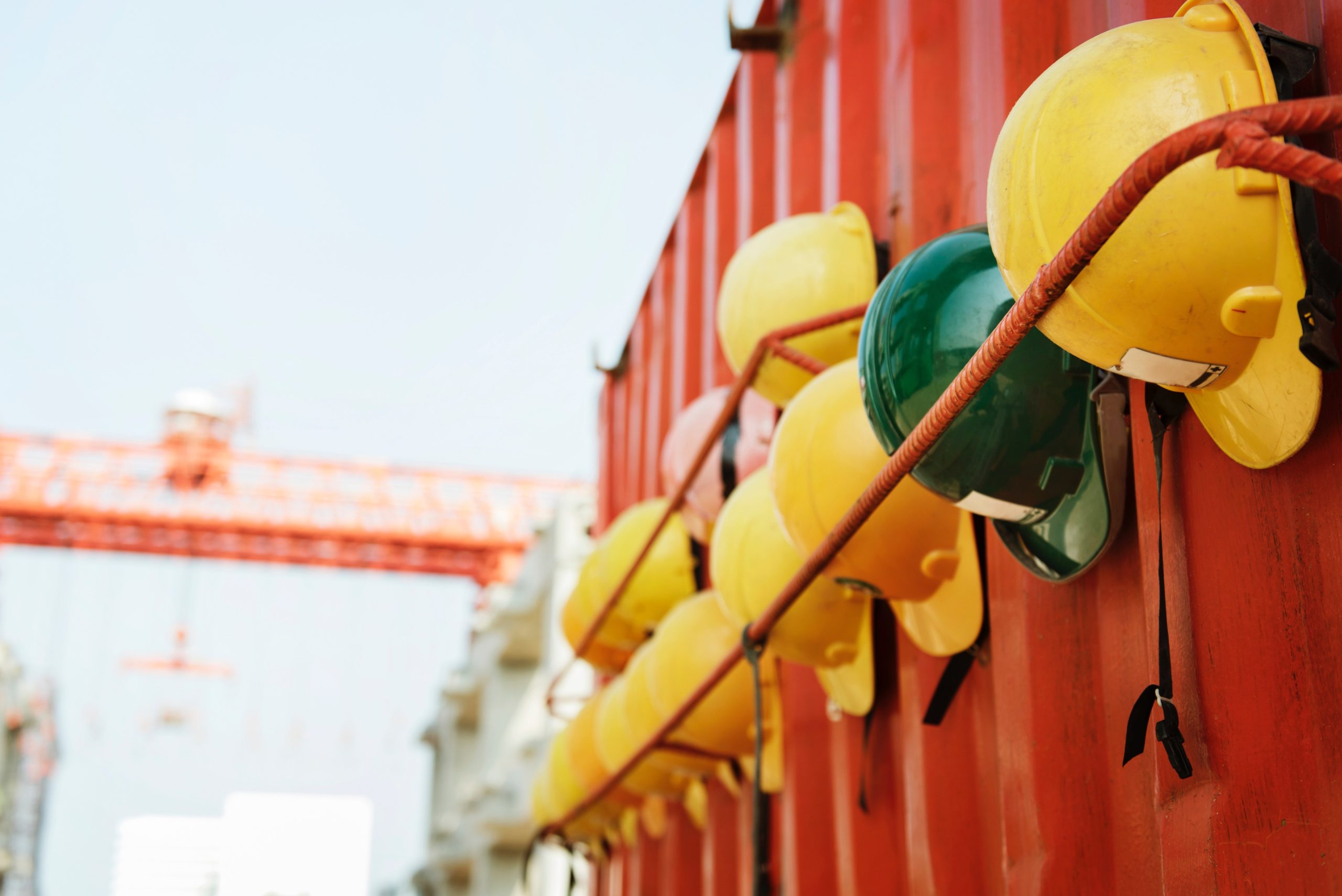
Safety Warning – Approach With Caution!
Are you responsible for managing asset hiring and interaction alongside your workshop and logistics teams? If those duties fall on your shoulders, you probably understand how a lack of plant, tool, and equipment visibility can pose a serious safety concern. Because many businesses struggle with accessing service history data, determining equipment safety can be a serious challenge.
And beyond equipment, what about people? If your business provides operators, it’s crucial that they possess the necessary qualifications to use plant and tools safely.
Safety is No Accident
Accident prevention hinges upon knowing asset and operator safety issues before they are put to work. Being keenly aware of possible safety concerns enables you to assess risks and plan accordingly. Log any and all safety issues into a digital database for record-keeping and maximum visibility.
Safety is never something that’s accidentally achieved. To that end, validating the compliance and certifications of your assets and operators is absolutely essential. Pre-planning and effective asset allocation are the key differentiators to all-around safety compliance.
Prevention and Visibility
Through automated notifications, reports and live analysis dashboards can provide real-time information, preemptive service alerts, and planned maintenance inspection reminders. Because these notifications are provided well in advance, your business won’t lose time or productivity when responding. By grouping reports and dashboards into a single system, you can empower your business with a single source of truth that’s visible to all and accessible on the go.
Nobody should have to use equipment that is out of test date or in danger of breaking down due to poor maintenance. By being attentive to your equipment’s upkeep demands, utilisation is likely to increase while accident frequency rate (AFR) and near misses decline.
Reduced Costs and Improved ROI
As you implement smarter safety and efficiency measures into your process, keep a close eye on how your assets and operators perform. Asset ROI and uptime should increase and so should your margins. In addition, your team won’t be pulling their hair out as much either. Thinking towards the future, you may even start to consider adding telematics and other smart technologies to your equipment to see how granular improvements can result in further savings.