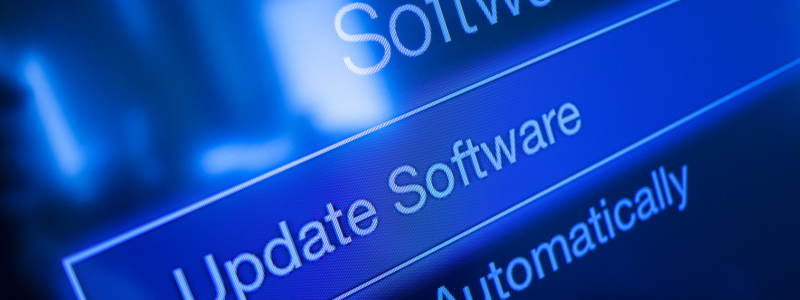
As the construction industry evolves, managing equipment efficiently becomes increasingly important. Many companies initially created in-house systems to handle asset tracking, maintenance, and workflow management. While these systems may have served well at the start, the fast pace of technological advancement now leaves many home-grown solutions struggling to keep up with the innovation leaps in specialized, customizable software. Surprisingly, while construction companies invest heavily in project management and accounting software, equipment management—the backbone driving those very projects—often gets left behind. This article explores the limitations of in-house systems and highlights the benefits of modern, purpose-built equipment management solutions.
The Overlooked Role of Equipment in Project Success
Project management and accounting systems are undeniably critical, but the role of equipment management is just as essential. Equipment costs can account for 30-40% of a project’s budget, meaning that inefficiencies directly impact overall profitability (Construction Dive). Underutilized or mismanaged equipment leads to cost overruns, downtime, and missed deadlines. Yet many companies, while focusing on other project tools, overlook the systems that manage their highest-cost assets. As Jane Black, a construction consultant with Construction Today, points out, “Construction companies often invest in project management tools but overlook the systems managing their highest-cost assets. Modern software aligns equipment management with overall project goals, driving better ROI” (Construction Today).
The Limitations of Home-Grown Systems
Though building an in-house equipment management system may have initially seemed attractive for its control and customization, several limitations often surface over time:
- Maintenance Burden on IT Teams: Keeping an in-house system up-to-date to meet industry standards can place a considerable burden on IT resources. According to Construction Executive, up to 70% of IT budgets in construction go toward maintenance, leaving little room for innovation (Construction Executive). This significant resource allocation restricts companies’ ability to focus on growth and operational improvements.
- Scalability Challenges: Home-grown systems may be suitable initially, but they often struggle to grow with the company. As project needs expand, the demand for integrating modern tools such as GPS tracking, data analytics, and telematics becomes critical. This often requires specialized expertise and resources, which many in-house IT teams cannot sustainably provide.
- Security and Compliance Risks: With the increasing rate of cyber threats, construction companies face heightened security demands. A Cybersecurity Ventures report projects that cybersecurity spending in construction will rise by 15% annually, as the sector becomes more vulnerable to attacks (Cybersecurity Ventures). In-house systems require ongoing updates and security checks to meet these demands—an overwhelming task for smaller teams focused primarily on operations.
- Limited Data Analytics for Strategic Decision-Making: Equipment management decisions should be data-driven, from assessing fleet performance to tracking utilization rates. Yet home-grown systems typically lack the advanced data analytics capabilities required for this depth of insight. According to a study by Deloitte, companies using data-driven insights for equipment decisions improved utilization by 20%, significantly reducing unnecessary costs (Deloitte).
The Benefits of Adopting Customizable, Purpose-Built Solutions
For companies recognizing the need for a dedicated, customizable equipment management solution, purpose-built software offers benefits beyond what a home-grown system can provide:
- Lower Long-Term Costs: Switching to a commercial software solution reduces long-term costs by removing the need for constant maintenance and updates. McKinsey reports that companies transitioning to industry-specific SaaS solutions saw a 30% decrease in IT expenses over five years (McKinsey). This reduction in maintenance costs allows teams to refocus on strategic priorities that enhance project outcomes.
- Automatic Upgrades and Innovation: With customizable software, companies can benefit from regular updates, ensuring their systems evolve with industry needs. “Purpose-built equipment management software helps construction companies reduce downtime and optimize usage, ultimately boosting project performance,” says Sarah Johnson, a construction technology specialist at Forbes (Forbes). By integrating telematics, mobile applications, and data analytics, these systems bring equipment management up to the same level of sophistication as other project functions.
- Future-Proofing Capabilities: Customizable software ensures that equipment management can adapt as project needs grow. Construction companies gain access to features like automated scheduling, predictive maintenance, and advanced tracking capabilities, which enable them to optimize fleet utilization and minimize costly downtime. Michael Anderson, an equipment management consultant with Industry Insights, emphasizes this, stating, “Investing in specialized software for equipment has become as essential as using project management tools. When equipment management integrates into broader project workflows, companies see real gains in productivity and cost control” (Industry Insights).
Industry Statistics Supporting the Shift to Purpose-Built Software
The construction industry’s shift to specialized asset management tools is increasingly evident. According to Deloitte, over 70% of large construction companies have adopted dedicated software for asset management (Deloitte 2024 Construction Industry Trends). This adoption reflects an understanding that equipment is more than an operational necessity; it’s a strategic asset that drives project outcomes and profitability.
Don’t Let Equipment Management Take a Back Seat
While project management and accounting systems remain central to construction operations, overlooking equipment management can be a costly oversight. Purpose-built, customizable solutions not only streamline processes but also align equipment management with broader project goals, leading to better ROI and a more competitive edge. By shifting from a home-grown system to a dedicated solution, companies can ensure their equipment contributes to project success as efficiently as other tools, transforming it from an operational afterthought into a core driver of productivity.
Thinking About Moving to a Purpose-Built Solution?
If you’re exploring a shift from an in-house system to a more comprehensive approach, RentalResult offers the tools to simplify equipment management and keep your projects on track. See how RentalResult can make the transition seamless, from streamlined tracking to better asset utilization.
Discover more about RentalResult and how it can support your team’s equipment management needs.