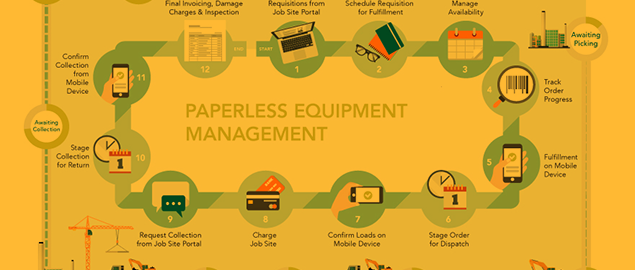
Would your construction business be nearer to utopia if all your equipment could be tracked and managed without using paper? If every job site could easily requisition equipment, every yard manage their inventory, maximize their delivery loads and drivers know where and when to deliver or pick up equipment? If that sounds too good to be true let me tell you how it could work.
The first step in the paperless nirvana, the Job Site Portal, we covered in last week’s blog. Basically, the Job Site Portal allows your job site personnel to requisition new equipment through a slick storefront program. They see a picture of equipment, details on it and the cost they will incur for use. Job site personnel choose the item, detail when they want it, where, and for how long and the request flows to the fulfillment team for processing. If they have ever ordered anything from Amazon, then they can easily use the Job Site Portal.
The fulfillment team then determines how they can fulfill the order. If it is coming from available equipment or being transferred from another site they can process the requisition internally and assign pickers and drivers to process the order. If they need to rent equipment they can send out a rental request to their preferred or multiple suppliers via email or electronically through the Supplier Connect to bid out the request.
Once the order is confirmed, pickers and drivers can be assigned as appropriate. Pick lists can be assigned to individuals or teams, orders can be split between trucks, multiple orders loaded on one truck, or separate journeys, whatever is the most appropriate.
Pickers and drivers will then view their assignments over a mobile app. There is no need for them to log into a computer, all the information they need is available to them electronically on their mobile app in the field. Once the yard and delivery duties are complete personnel can simply sign off via the app and all can see what is completed. At delivery, the drivers can detail delivery times and collect signatures confirming the delivery.
Invoices can be created or internal costs calculated when the equipment is delivered. Details are sent electronically or posted to corporate financial packages like Oracle, SAP or JD Edwards. Everyone has visibility to the charges at each step of the process, which reduces discrepancies at month end.
When the equipment is ready to be picked up the reverse process begins. The job site requests off-rent via the Job Site Portal, the fulfillment team processes the request, drivers receive instructions over the mobile app to pick up the equipment. Drivers then note the equipment condition, collect signatures and document the date and time of the pickup on their mobile device. And then the billing is complete and any damage changes added.
This completes the full circle or equipment from requisition to return, all without using paper! If you are interested in learning more about a paperless process let us know.