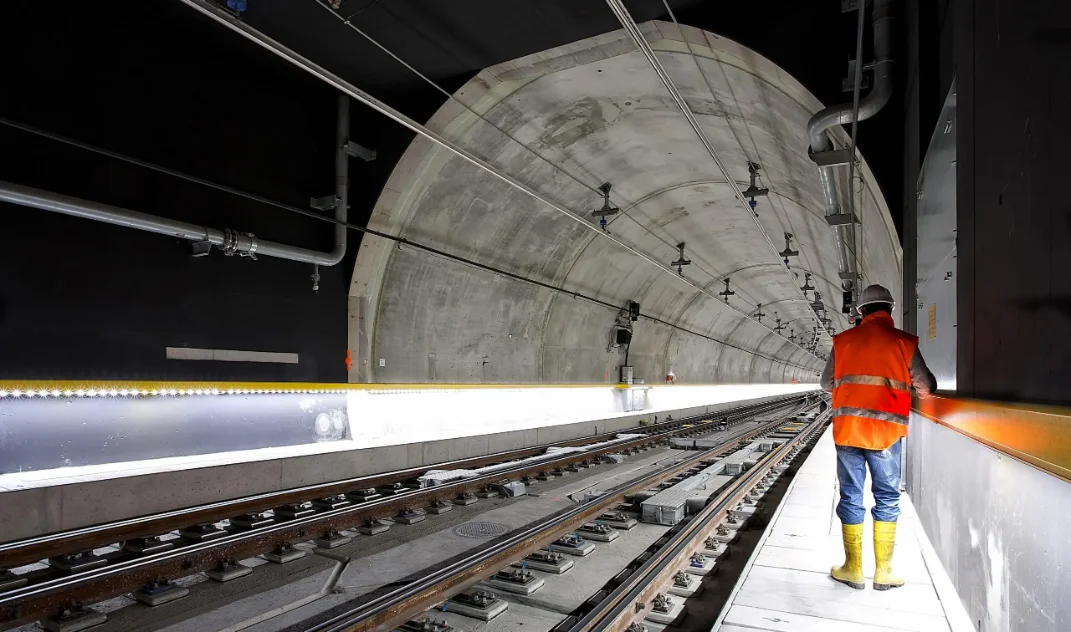
Because Safety is No Accident
Site safety and risk management is and has always been at the forefront of any contractor or hire company’s agenda. You go to work safe and get home safe…Simple!
Follow these 8 simple steps to help utilize your plant hire software effectively to improve safety.
1: Restrict non-compliant assets. Use your software to restrict or warn you when selecting an asset that has certificate or other date driven requirements, such as routine inspections, which has expired or will expire in the life of the hire contract to promote and drive safety initiatives.
2: Automate safety sheet distribution. Use your software to auto generate safety sheets or instructions for contracts based on the equipment being hired so they automatically email or print with the contract.
3: Ensure safety features aren’t missed. Set up mandatory accessories or attachments to go along with the main item being hired that are vital to its safe use. For example, slew restrictors, parabolic mirrors or beacons might not be charged for as separate items, but can be detached from the item. If it’s setup as a mandatory free accessory that is only visible internally, it provides a reminder to the person fulfilling the order that all parts need to be sent. This helps ensuring all safety features of the hired equipment are included
4: Prevent hire of unchecked equipment. Prevent equipment from being hired out until it’s been fully inspected after the last hire by using the system statuses and automatic creation of service orders for the checks to be performed.
5: Send only qualified operators. Ensure the operator you are sending out is qualified to operate that specific piece of plant. Competencies can be set up in the system against plant, as well as defined against operators to ensure the right operator is sent out and safety is up-held.
6: Verbal instructions. Set up warning messages that are linked to equipment types and will appear when adding lines to a contract for the hire coordinator to advise the hirer. Sometimes they might trigger the hirer to realise they might need a different piece of equipment or additional safety equipment.
7: Ensure the right equipment is dispatched. Try using a list of key questions that can be asked when raising the hire contract to ensure the right equipment is selected for the job. For example, something incapable of dealing with the power capacity required might cause fires, so its wise to check before you incur the expense of sending it to site and the risk with having the wrong thing in the wrong place.
8: Be proactive about compliance and safety checks. Using the system reminders and schedules to ensure checks and services are being performed and on time to keep equipment in the best and safest shape. You can also use this information to make sure that the assets sent out to site are going to be OK to run for the whole of the hire and you won’t have to manage expensive field servicing to keep the asset running at the job site.
Safety management requires every tool in your arsenal. Make sure your plant hire software is one of your tools to help keep your team safe and accident-free.