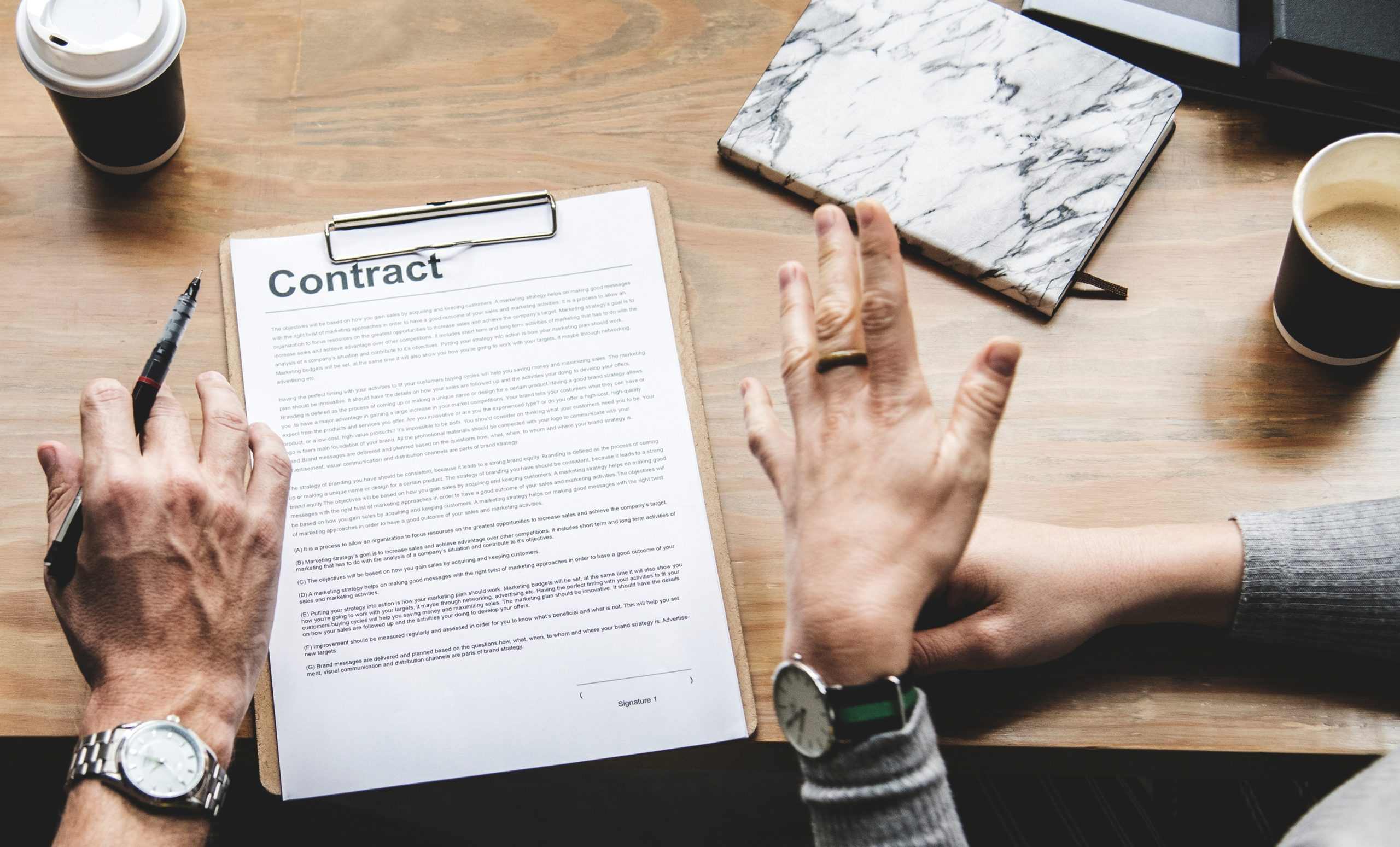
If you’ve ever had the pleasure of buying windows or doors, you know the process starts with a sales visit. A sales rep arrives at your home, drinks their body-weight in tea, and generally makes you wonder if they will ever leave. It’s a time-honoured tradition. Eventually though, after taking some measurements, drawing a picture, and filling out a paper work sheet, the rep hand-types your desired products into an order form.
No apps or online tools were used or harmed in the process.
What’s Wrong With Paper Processes?
Based on the initial requisition, there’s nothing wrong with paper processes. As far as I knew, the rep recorded everything correctly and my order was taken care of. It’s what happened next that inspired me to write this blog.
My Paper Process Horror Story
Once they returned to their office, my rep wrote up a works order form for their manufacturing team. Unfortunately, when manually duplicating what they originally wrote onto another paper document, disaster struck. They entered the wrong window glass and completely left off a door and window sill!
From this blunder, two incorrect paper forms were then handed from manufacturing to transport and the fitters. While the errors were identified once on site, they still resulted in a large delay. A paper rectification report had to be created and a revisit (at the cost to the supplier) had to be arranged. Frustrating to say the least.
On top of all this, when the fitters returned, the door they brought was built incorrectly. This resulted from the supplier not having access to the original paper drawing. To correct this, a third rectification visit was needed, again at cost to the supplier.
The Better Alternative
The morale to this story is that a simple mobile app could’ve spared everyone from these headaches. Through apps, requisitions can be easily sent to a supplier before being converted to an order. From there, tracking is easily done through the build stage to picking and dispatch. Automatic notifications to on-site fitters help prevent human errors endemic to overly complicated manual processes.
Small mistakes can snowball into big costs for businesses. Margins, time, and resources were all negatively impacted in my example alone.
So when it comes to paper versus paperless, is there even a contest?